Self-Healing Material
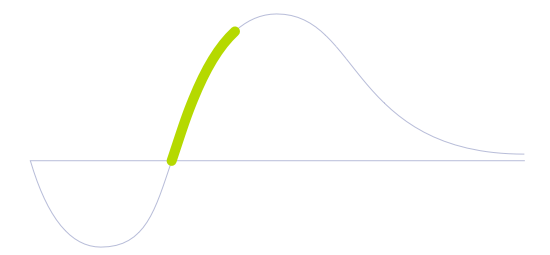
Technology Life Cycle
Marked by a rapid increase in technology adoption and market expansion. Innovations are refined, production costs decrease, and the technology gains widespread acceptance and use.
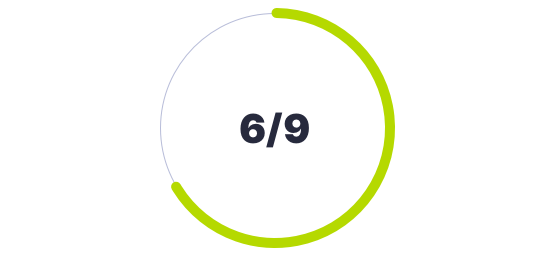
Technology Readiness Level (TRL)
Prototype is fully functional and ready for testing in industrially relevant environment.
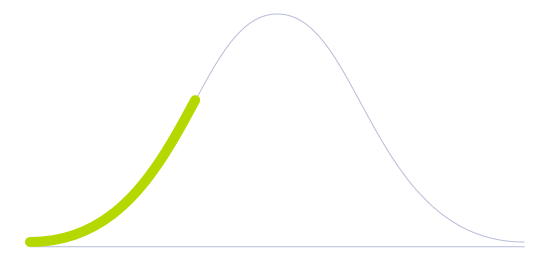
Technology Diffusion
Embrace new technologies soon after Innovators. They often have significant influence within their social circles and help validate the practicality of innovations.
Microcracks and hidden damage are the causes of structural failures. With the ability to repair themselves automatically without an external diagnosis or any human intervention or external stimuli, such as heat or light, these artificially and synthetically created materials use a variety of self-repair techniques such as forming hydrogen bonds, metal-ligand coordination, or even ion-dipole interactions. They mimic biological systems that can repair and regenerate damaged tissue.
The specific mechanisms of self-healing materials vary depending on the material and application, with some having microcapsules or fibers that release a healing agent when the material is damaged, while others have a network of microchannels that distribute the healing agent throughout the material. Additionally, some self-healing materials undergo reversible chemical reactions that allow them to repair themselves when damaged.
A variety of classes of materials, including metals, glass, rubber, silicon, cotton, leather, ceramics, concrete, and polymers, are a few examples of tested self-healing components. However, a polar, stretchable polymer, poly (vinylidene fluoride-co-hexafluoropropylene), and a mobile ionic salt is the most popular combination among scientists to produce a self-healing material. It works through a chain linked to an ion-dipole interaction between the polar groups in the polymer and ionic salt. The result is a technology based on polymeric material, useful for self-repairing electronics, soft robotics, or even liquid coatings that could make for cleaner and less sticky furniture, automotive interiors, clothing, shoes, handbags, etc. This technology could create water-resistant and super-liquiphobic products, repelling both water and oil-based liquids.
Self-healing materials have a wide range of applications in industries such as aerospace, automotive, construction, and electronics. They can reduce maintenance costs, extend the lifespan of products, and improve safety by preventing catastrophic failures. Self-healing materials can also prevent catastrophic failures in critical components, such as aerospace components, and improve the durability of products like electronics and automotive components, reducing the need for replacement and repair.
Future Perspectives
Self-healing materials/composites will soon have a significant impact, especially for materials such as underwater piping or even aerospace structures, where maintenance and inspection are nearly impossible due to inaccessibility. With self-healing capabilities, there would be no concerns over issues such as erosion or microcracking. It could be possible for these principles to be applied to the development of lithium batteries, artificial muscles, fixing broken smartphones, or even avoiding oil spillage and loss of water due to faulty pipes.
Image generated by Envisioning using Midjourney