Remanufacturing
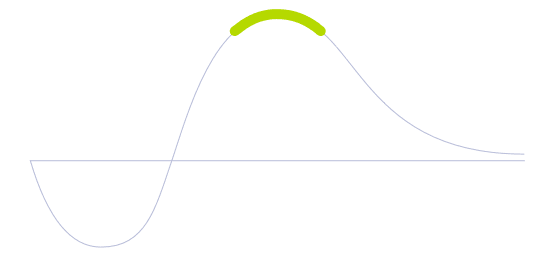
Technology Life Cycle
Sales growth slows as the market becomes saturated. The technology is well-established and competition peaks, leading to price drops and marginal improvements.
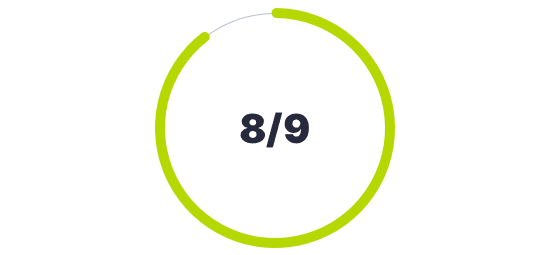
Technology Readiness Level (TRL)
Technology is developed and qualified. It is readily available for implementation but the market is not entirely familiar with the technology.
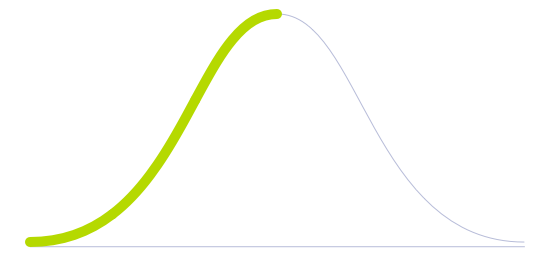
Technology Diffusion
Adopts technologies once they are proven by Early Adopters. They prefer technologies that are well established and reliable.
Nowadays, buying a new product has become cheaper and more accessible than fixing a broken one. The complexity of products is so high that the average consumer has no in-depth knowledge of how these devices work. This situation creates sizable environmental issues because it forces the consumer to discard products simply because one part is malfunctioning, thereby producing significant amounts of very persistent waste. The remanufacturing process helps thwart waste production by reducing the consumption of raw materials, water, and electricity and the emissions of greenhouse gasses in the supply chain.
Classical remanufacturing of consumer products realized by manufacturers involves repairing a used, malfunctioning product under warranty to its original performance, equivalent to that of the newly manufactured product. The process begins with a technician or machine dismantling the product, then analyzing, restoring, and replacing damaged components. The technician then tests both the individual parts and fully-assembled items to check if the functionality is in line with the original design specifications. The point is to fix broken products instead of simply discarding them. From a customer viewpoint, the remanufactured product is roughly equivalent to a new product.
Remanufacturing is an essential component of developing resource-efficient manufacturing industries. By maintaining and using parts and materials for an extended period, society can avoid emitting more greenhouse gasses, polluting the air and water, and significantly reduce the manufacturing impact of energy use and waste production. In addition to environmental benefits, remanufacturing provides opportunities to create highly skilled jobs and economic growth. By saving more resources, firms could become more competitive, mostly if bureaucratic restrictions required companies to offset the ecological consequences of their business practices.
Remanufacturing strategies include:
- Reuse - disassembling broken gadgets to harvest usable parts for installation in newly manufactured products.
- Remanufacturing - used products restored to new-like condition after being disassembled, cleaned, inspected, and reassembled, optionally creating opportunities for products to be updated in the process.
- Reconditioning - parts or components are cleaned and repaired for reuse or resale afterward.
- Component Cannibalization - a limited number of components can be extracted for a single product. The excess parts can be used to repair or rebuild another unit at the malfunctioning item's expense.
- Material Recycling - the reprocessing of materials to return to their raw form, so they can be used as a "new" material for manufacturing a new product.
By beginning to think about product remanufacturing possibilities, designers are already considering methodologies that include modularization, reuse of returned parts, life cycle profit, customized remanufactured products, upgradeability, and reusability evaluation quota, use of sustainable remanufactured products, and analysis of re-manufacturability. In other words, even before creating a product, engineers and designers are already considering the degree of reusability and re-manufacturability of components, forming a more conscious cycle of production and consumption in a closer move to a closed-loop system.
Finally, there are alternatives that the manufacturer does not need to be involved in; third-party repair shops or the consumers themselves could carry out the remanufacturing. Repair-friendly regulations would need to be enacted and enforced (e.g., the "right to repair" initiative in the United States and European Union), ensuring easy-to-disassemble products with an abundance of spare parts available to replace broken ones. This initiative could include making systems more modular, developing repair manuals, and determining the average expected lifetime of individual components.
Future Perspectives
20th-century material extraction increased exponentially due to many industrial revolutions creating a production paradigm in the industrial sector. Accordingly, as the population grows, resource consumption is expected to continue to rise significantly. Thinking in circular economy terms, this business model could create a way that can dramatically reduce the strain on resources.
Society needs to invest in methods of extending product lifespans to close the loop. This would be accomplished mainly by using fewer resources, focusing primarily on reuse, repair, refurbishing, and remanufacturing. These practices can go a long way, especially when combined with new community-based exchange platforms, decentralized production, and innovations in transportation, mobility, and 3D printing.
Image generated by Envisioning using Midjourney