Flexible Electronics
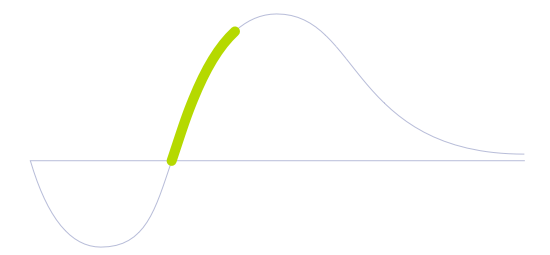
Technology Life Cycle
Marked by a rapid increase in technology adoption and market expansion. Innovations are refined, production costs decrease, and the technology gains widespread acceptance and use.
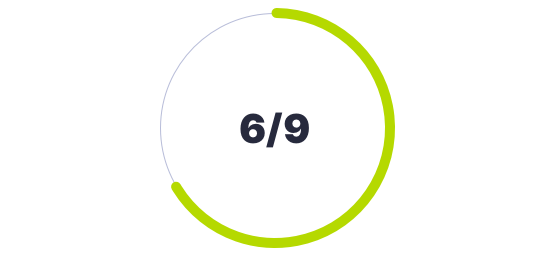
Technology Readiness Level (TRL)
Prototype is fully functional and ready for testing in industrially relevant environment.
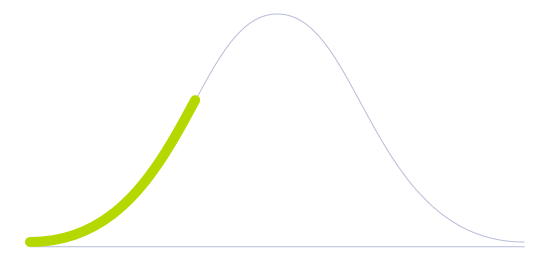
Technology Diffusion
Embrace new technologies soon after Innovators. They often have significant influence within their social circles and help validate the practicality of innovations.
Flexible Electronics are electronic devices built on flexible materials — such as polymers, plastic, metal foil, paper, smart textiles, flex glass, or thin films — as their base, allowing them to conform to different shapes and contours. Unlike traditional rigid electronics, Flexible Electronics can be stretched, bent, folded, or rolled without losing functionality.
Flexible Electronics involve the use of specialized materials and manufacturing processes. Conductive polymers or thin metal films, for instance, are utilized to create flexible circuits and interconnections, which allow them to maintain conductivity properties even under mechanical strain. Other electronic components, such as transistors, organic semiconductors, sensors, batteries, or displays, can be fabricated using flexible materials or a hybrid of flexible substrates. Flex circuits can be manufactured by laying conductive lines using one of several printing methods, including screen, inkjet, gravure, or 3D-printing techniques.
As Flexible Electronics enable the development of devices that can conform to various shapes and surfaces, new design possibilities appear, allowing seamless integration into unconventional forms. Such versatility is valuable in wearable electronics, allowing devices like smartwatches, fitness trackers, or electronic textiles to comfortably adapt to the body's movements. The flexibility of these electronics also makes them more resilient to mechanical stress and shock, reducing the risk of damage from impacts or vibrations. This enhanced durability is crucial for applications in harsh environments, such as aerospace or automotive industries, where traditional rigid electronics may not withstand extreme conditions. Furthermore, Flexible Electronics solve the problem of limited space. With their ability to be thin and conform to tight spaces, these devices can be integrated into compact and resource-constrained environments, such as medical implants, electronic skin, or Internet of Things (IoT) sensors.
Future Perspectives
By overcoming the limitations of today's rigid electronics, Flexible Electronics pave the way for a future where electronic devices seamlessly integrate into our everyday lives, offering enhanced comfort, functionality, and durability. As this technology becomes mainstream, the IoT could become even more invisible, and the line between the digital and concrete worlds will be further blurred.
Flexible Electronics could be integrated into clothing, accessories, or infrastructure to capture and convert ambient energy, such as body heat, motion, or light, into electrical energy for powering wearable devices or IoT sensors. Also, Flexible Electronics integrated into packaging materials could enable interactive and intelligent packaging solutions. This could include features such as freshness monitoring, product tracking, personalized information, enhancing consumer experience, and supply chain management.
Image generated by Envisioning using Midjourney